What is a rotary encoder?
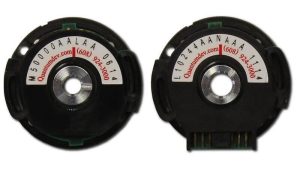
QM35 (left) & QML35 (right) rotary encoders with bearingless modular design
A rotary encoder is an electromechanical device that attaches to a motor/shaft assembly in order to accurately report the position, speed and acceleration of the rotary shaft. The rotary encoder (aka shaft encoder) senses the angular position and motion of the rotary shaft and generates digital output signals based on those rotational mechanical displacements. In contrast, linear encoders detect mechanical displacement along a straight line.
On this page:
Types of rotary encoder
There are two main types of rotary encoder: incremental and absolute.
Incremental rotary encoders report changes in position, or relative position. Motion controlled systems using incremental rotary encoders need to be “homed in” on startup, or after a power loss. See: How Incremental Encoders Work
Absolute rotary encoders are able to report position information as soon as they’re powered up, even if power was interrupted during the last use. No calibration is necessary to find the absolute (starting) position, which is always known.
There are also three main types of technologies for rotary encoders:
Optical
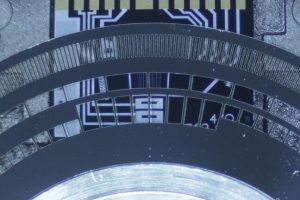
Magnified view of optical incremental rotary encoder disc and photosensor
Optical rotary encoders have an LED light source, a spinning disc with slot-like openings, and a photosensor. As the disc turns with the shaft rotation it creates light pulses which are translated into digital square waveforms by an electronic circuit. See: How Optical Encoders Work
Mechanical
Mechanical rotary encoders (aka conductive encoders) use concentric copper rings and contact brushes to create a positionally encoded conduction that can be read by an electronic circuit.
Magnetic
Magnetic rotary encoders have a rotating wheel with a series of magnetic poles around it. As the wheel rotates it passes by a circuit that senses magnetic field changes and converts the feedback into a digital output signal.
Quantum Devices designs and manufactures high-performance incremental optical rotary encoders ideal for many different industries and applications.
Rotary encoder uses
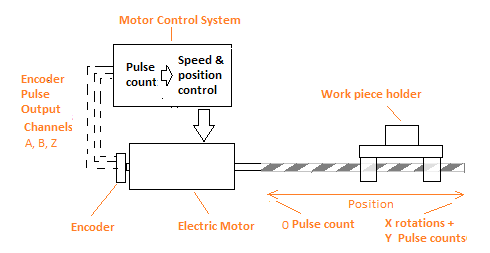
Rotary encoder mounted directly to the electric motor shaft
Rotary encoders are used to monitor and/or control a wide range of mechanical systems. For example, rotary encoders are used in industrial automation to control conveyor belt speed and direction.
Rotary encoders are also used for servo motor feedback, to control speed as well as multiple axes of motion. Rotary encoders are mounted directly to the motor shaft in packaging/labeling machines, textile machinery and material handling equipment.
Additional rotary encoder applications include AGVs, flight simulators, dosing pumps and many others. Quantum Devices partners with OEM equipment manufacturers to provide application-specific encoders, with free samples available for qualified projects.
Choosing a rotary encoder
Assuming you’ve determined whether your application requires an absolute or incremental rotary encoder, the primary considerations when selecting a rotary encoder are the size and shaft type.
Size
You’ll need to know the space requirements of the system where your rotary encoder will be integrated.
Critical measurements include:
- Housing diameter
- Housing profile (height)
- Shaft/bore diameter
Shaft Style
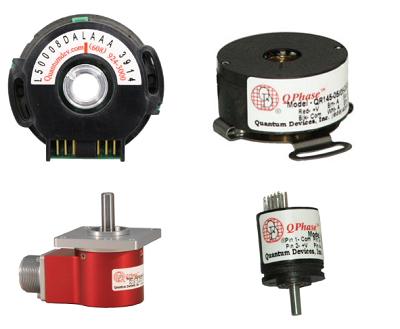
Rotary encoders with hollow or solid shaft & different housings
Rotary encoders can have a solid or hollow shaft, and which type you need depends on the incoming shaft type in your application. It’s also important to choose the right fittings and mounting arrangement to ensure proper alignment.
Environment
Once you’ve defined the mechanical specifications for your rotary encoder, you’ll also need to consider the operating environment. The effects of dust, vibration, temperature extremes, moisture and other contaminants can be mitigated by choosing a rotary encoder designed to operate under demanding conditions.
Resolution
Resolution refers to the smallest unit of measure the encoder can detect. For rotary encoders, resolution is the number of pulses per revolution (PPR). Not all applications require the same level of positioning accuracy, and the maximum input frequency of the encoder’s controller is also a factor. For more detail, see our page on choosing the resolution of a rotary encoder.
Quantum Devices sales engineers are happy to assist in encoder selection. Contact us online or call (608) 924-3000 for expert help.
Why do rotary encoders fail?
When rotary encoders fail to perform, the most common causes stem from mechanical or environmental problems.
Bent Shaft
When a shaft is bent it becomes misaligned with the bearings. This displacement puts more stress on the bearings and can lead to overload or overheating. It’s important to adhere to the specified mounting tolerances and installation instructions.
Contamination
In harsh environments, temperature changes or direct contact with liquid can introduce humidity into the encoder housing. The resulting condensation on the disc, PCB or wiring can cause encoder failure. Dust and other particulates inside the encoder can cause optical technology to fail.
Signal Issues
Signal output failure can be caused by several different mechanical or environmental factors including mounting issues, shorted wires, crosstalk, signal interpolation or output driver issues. Check out our guide to troubleshooting encoder noise problems.
Stuck on an encoder problem? Our engineers are happy to provide a review of your application or help you troubleshoot rotary encoder failure.
Better Design, Better Performance
Quantum Devices rotary encoders perform better than the competition because of important mechanical and electrical differences in our design and component quality. See our detailed technical comparison of encoder products for more information.
Rotary Encoder Supplier
Quantum Devices is a vertically integrated encoder manufacturer providing high quality rotary encoders to OEMS in many different industries. We offer a variety of rotary encoders including miniature, industrial, waterproof, programmable, low-profile, hollow shaft, shafted, bearing and modular encoders. We can customize any encoder for your application.
Our products are made entirely in the USA and backed by a 2-year warranty.
Whether you need a custom rotary encoder or an evaluation unit for research and development, we can help. Get in touch with your requirements and our engineers will find a solution.